Electric Traction
The basis of a successful electric traction concept is the right choice and design of the motor, its power supply and control. Modern electric drives are subject of high demands in terms of efficiency, reliability, noise and cost. In order to achieve the optimum drive for the application, it is necessary to take into account the real working conditions and demands placed on the drive. We deal with the complete design process from the definition of the requirements for the electric motor, its electromagnetic and thermal design, optimization and its construction.
Definition of drive requirements - selection of suitable electric motor type
For correct dimensioning of the motor, the power and torque requirements for the motor must be defined as precisely as possible. To obtain them, TechSim use 1D system simulations. By that means, the drive can be tested for real working conditions (based on the customer's driving data) to obtain a real load behavior in the early stages of the development. At the same time, due to the low numerical complexity of the system simulation, it is possible to test a large number of variants and different strategies and compare them with each other. Components of the drive can be selected correctly and design errors can be avoided. The following parameters can be determined, obtained and verified in 1D system simulations:
Offered Solution | Analysis Type | Software | |
---|---|---|---|
Optimization of parameters of any component, e.g. electric motor, gearbox or battery pack. | 1D | Simcenter Amesim | |
Test the drive for given load cycles or accelerations | 1D | Simcenter Amesim | |
Determination of the influence of the battery source on the drive | 1D | Simcenter Amesim | |
Sizing the drive cooling circuit | 1D 3D CFD 3D CFD |
Simcenter Amesim Simcenter STAR-CCM+ |
|
Determination of final energy balance of the system and its losses | 1D | Simcenter Amesim |
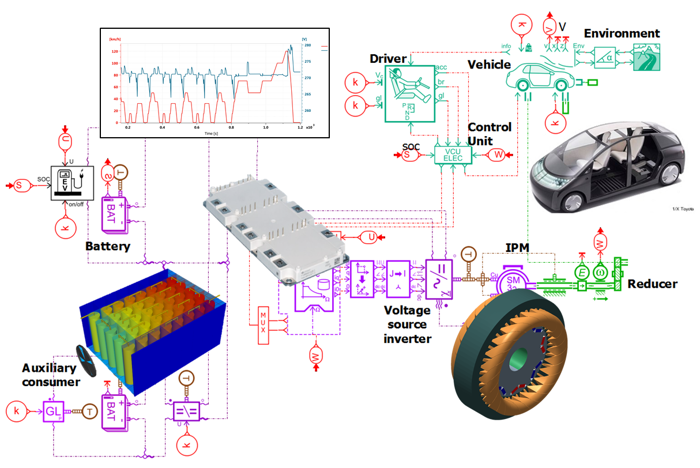
Demonstration of the electric vehicle system simulation (EV)
Electromagnetic design and optimization of electric motor
TechSim offers the design and optimization of all types of electric motors. Design is done by finite element method (FEM) simulation. The goal of these simulations is to create the best design suited for a given application. The specific objective of the analysis may be, for example:
- Reducing losses, increasing efficiency
- Reduction of noise and ripple torque
- Increase of maximum moment and performance
- Cost reduction
Furthermore, it is possible to verify the parameters of already designed electric motors using simulations and to detect design errors. The following programs are used for electromagnetic design of the electric motor and its optimization:
Offered Solution | Analysis Type | Software |
---|---|---|
Electromagnetic design and optimization of all types of motors and generators | 2D FEM | Simcenter MotorSolve |
Analysis of electric motor performance parameters and its losses | 2D FEM 2D FEM |
Simcenter MotorSolve |
Accelerated engine cooling calculation | 2D FEM | Simcenter MotorSolve |
Detailed electromagnetic calculation of electric motor | 3D FEM | Simcenter Magnet |
Detailed calculation of engine losses and cooling | 3D FEM 3D FEM 3D CFD |
Simcenter MotorSolve Simcenter Magnet Simcenter STAR CCM+ |
Demonstration of results: efficiency map, loss distribution, magnetic field distribution.
Design of electric motor
In cooperation with our partner companies, we are able to mediate the design of our electric motor, to provide relevant drawing documentation based on the manufacturer's technological procedures.
Cooling design and optimization
Proper cooling is the next chapter in the design of electric motors, especially with the aim of the best power / weight ratio. Simulation of electric motor cooling is a problem, where many aspects need to be considered. First, it is necessary to correctly determine the losses of the electric motor, i.e. the heat source. These are obtained as a result of electromagnetic analysis of the electric motor. The heat generated is further propagated by conduction in solids, which can be calculated by the finite element method (FEM), and further the heat is dissipated by free convection, radiation or through the cooling medium in the cooling ducts away from the electric motor. Fluid flow is calculated using the fluid flow dynamics (CFD) calculation method. Moreover, the individual analyses (loss calculation, heat conduction, flow) influence each other and it is therefore necessary to interconnect them.
We provide a complete calculation of electric motor cooling including CFD method. We also perform a simplified calculation of the FEA cooling method, where the flow is replaced by analytical-empirical relations.
Calculation of temperature fields of electric motor and heat dissipation into surroundings.